Overcoming Information Silos Problems in Farming Equipment Repair
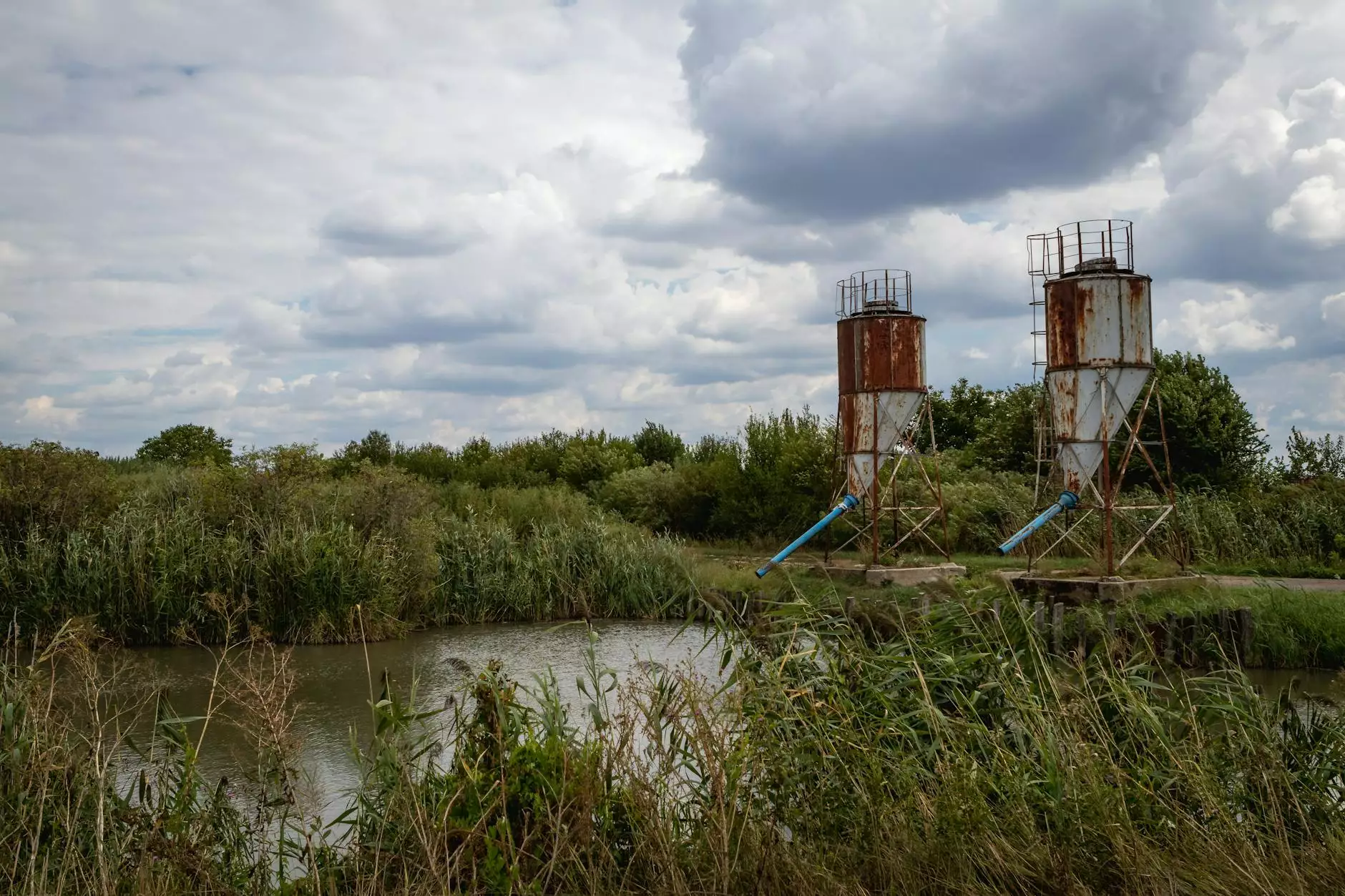
In the dynamic and ever-evolving landscape of modern agriculture, information silos problems pose significant challenges. These issues not only hinder communication and collaboration within organizations but also impede the efficiency of farming equipment repair. As we delve into the core of these challenges, it becomes pertinent to understand their origins, impacts, and ultimately, the empowering solutions that pave the way for streamlined operations and improved productivity.
What are Information Silos?
Information silos refer to the discrete collections of data or information that exist within different departments or teams of an organization. These silos often prevent critical information from flowing freely across an organization, leading to fragmented knowledge, duplicated efforts, and a lack of cohesion in business strategy and execution. In the context of farming equipment repair, the presence of such silos can have detrimental effects on operational efficiency and customer satisfaction.
The Origins of Information Silos Problems
The formation of information silos is not an overnight occurrence. Several factors contribute to the establishment of these barriers within organizations, particularly in the agriculture sector. Here are some key contributors:
- Departmentalization: As businesses grow, they tend to segment into specialized departments. While this fosters expertise, it can also lead to disjointed operations where teams operate independently without sufficient communication.
- Technological Barriers: Utilizing disparate software systems can result in data fragmentation. For instance, a repair department using one system may not easily share information with the sales team operating on another platform.
- Cultural Factors: An organizational culture that does not promote collaboration can lead to entrenched silos, where employees prioritize their department’s interests over the broader company goals.
- Lack of Standardized Processes: Without clear, standardized procedures for data sharing and communication, teams may inadvertently isolate themselves.
Consequences of Information Silos in Farming Equipment Repair
The repercussions of information silos problems can be extensive. For businesses involved in farming equipment repair, these silos can manifest in various detrimental ways:
- Reduced Efficiency: When information is not shared effectively, workflows can become bottlenecked, slowing down repair times and frustrating both employees and customers.
- Inaccurate Data: Disparate systems may lead to outdated or incorrect information being utilized, resulting in poor decision-making and additional costs due to errors.
- Poor Customer Service: If repair teams lack access to relevant customer or equipment history due to siloed information, it can lead to unsatisfactory service and decreased customer loyalty.
- Increased Costs: Redundant efforts across departments can inflate operational costs. Each department may be duplicating work instead of collaborating efficiently.
Solutions to Break Down Information Silos
Tackling the challenge of information silos problems is crucial for fostering a cohesive and efficient workplace. Here are some effective strategies for dismantling these barriers within your organization:
1. Foster a Collaborative Culture
The first step in combating information silos is to cultivate a culture of collaboration. This involves encouraging communication across departments, organizing cross-functional teams, and celebrating shared successes.
2. Implement Integrated Technology Solutions
Utilize integrated software systems that allow for seamless information sharing across departments. For instance, adopting a Customer Relationship Management (CRM) system that can interface with repair management tools ensures all relevant data is accessible in real-time.
3. Standardize Communication Protocols
Establishing standard operating procedures (SOPs) for communication can facilitate improved information flow. Use collaborative tools such as shared dashboards or project management software to keep all teams aligned.
4. Provide Training & Development
Educating employees on the importance of communication and collaboration is vital. Regular training sessions can emphasize the value of shared information and how it contributes to improved outcomes in farming equipment repair.
5. Lead by Example
Leadership plays a pivotal role in breaking down silos. Leaders should model collaborative behavior by engaging with various teams, promoting open lines of communication, and showing how teamwork drives success.
The Role of Data Analytics in Overcoming Information Silos
Data analytics can be a powerful ally in overcoming information silos. By harnessing analytics tools, organizations can:
- Identify Gaps: Analyzing data across departments can help pinpoint where information is lacking or where there is redundance.
- Predict Trends: With access to a comprehensive data set, teams can better forecast equipment failures or maintenance needs, leading to more proactive service.
- Enhance Decision-Making: Analytics can provide insights that inform strategic decisions, ensuring that all departments are aligned with the company’s goals.
Real-Life Examples of Successful Integration
Numerous businesses have effectively addressed information silos problems, leading to remarkable improvements in operational efficiency. Here are a couple of case studies illustrating successful integration:
Case Study 1: AgriTech Solutions
AgriTech Solutions, a leading provider of farming equipment, faced significant delays in their repair services due to siloed information across departments. By implementing a centralized ERP system, they facilitated real-time data sharing, resulting in a 30% reduction in repair turnaround time and a marked increase in customer satisfaction. Their cross-departmental training sessions further strengthened collaboration, ultimately leading to a more harmonious workplace.
Case Study 2: Greenfields Equipment
Greenfields Equipment is another example where addressing information silos led to success. They employed data analytics to unify repair and customer service data, which helped them identify common repair issues. This proactive approach not only minimized downtime for their clients but also enabled their sales team to upsell preventive maintenance services effectively, leading to an increase in overall sales.
Conclusion: A Unified Approach for Enhanced Future Operations
In an era where data is paramount, overcoming information silos problems is not just beneficial; it is essential for organizations in the farming equipment repair sector. By fostering collaboration, integrating technology, and promoting a culture of shared success, businesses can not only enhance their operational efficiency but also improve customer satisfaction and loyalty.
As we continue to navigate the future of agriculture, let us commit to breaking down the barriers that inhibit progress. Embrace the potential that lies in a unified approach, for in collaboration, we find the strength to transform challenges into opportunities.